この記事では、硬質クロムメッキの基礎から応用までを掘り下げ、そのメリットやデメリット、工程、さらにはJISの品質基準に至るまで詳細に解説します。
硬質クロムメッキがどのようにして部品の寿命を延ばし、性能を向上させるのか、また、そのプロセスがどのように精密に管理されているのかを理解することで、この技術がなぜ多くの産業分野で不可欠とされているのかが明らかになります。
硬質クロムメッキとは?
硬質クロムメッキは、クロム金属が1μm以上メッキされたものであり、耐摩耗性や硬度に優れています。一般的には工業製品に使用され、摺動部や可動部の部品、機械部品、金型などに適しています。
めっき液中の六価クロムが製品近傍のマイナス極で還元されて三価クロムに替わり、その三価クロムが硫酸とめっき可能な三価クロム化合物に変化し、めっき液のもともとの成分に含まれていないはずの三価クロムは製品表面で生成されます。
クロムメッキの分類
一般にクロムメッキには「装飾クロムメッキ」と「硬質クロムメッキ」の2種類があります。
装飾クロムメッキ
装飾クロムメッキは、その名の通り、主に美観を高める目的で用いられます。オートバイのエキゾーストパイプ、自動車のバンパーやリム、キッチン用品やバスルームのアクセサリーなど、日常生活の様々な製品に見ることができます。
装飾クロムメッキの最大の特徴はその輝きです。非常に滑らかで鏡のような表面は、製品に高級感を与えるだけでなく、清潔感も演出します。膜厚は通常0.5〜1.0ミクロン程度で、非常に薄いため、下地の状態が表面に直接影響します。そのため、メッキ前の研磨や下地処理が非常に重要となります。
さらに、装飾クロムメッキは耐腐食性にも優れており、製品の耐久性を高める効果もあります。ただし、その耐久性を維持するためには、定期的な清掃と適切なメンテナンスが必要です。
硬質クロムメッキ
一方、硬質クロムメッキは工業分野でその真価を発揮します。特に高い硬度を必要とする部品や、摩擦や摩耗が激しい環境下で使用される部品に適用されます。
硬質クロムメッキの層は通常、20ミクロンから300ミクロンの範囲で、装飾クロムメッキよりもはるかに厚く施されます。これにより、メッキされた部品は非常に硬く、耐摩耗性に優れます。また、高い耐熱性や耐腐食性もこのメッキ方法の重要な特徴です。
硬質クロムメッキは、エンジン部品、油圧ピストン、金型など、厳しい使用条件下での性能が求められる多くのアプリケーションで採用されています。このメッキ方法のもう一つの重要な利点は、部品の寸法精度を向上させることができる点です。厚いクロム層は、基材の表面の微小な欠陥を覆い隠し、滑らかで均一な表面を実現します。これは、高精度を要求される部品の製造において非常に重要です。
硬質クロムメッキの特徴・メリット
以下に、硬質クロムメッキが提供する主な特徴とメリットを詳細に解説します。
高硬度
硬質クロムメッキの最大の特徴はその非常に高い硬度です。クロムメッキ層は硬度が非常に高く、部品の表面を非常に耐摩耗性が高いものに変えることができます。この高硬度は、特に摩耗が激しい環境で使用される部品にとって重要です。硬質クロムメッキを施した部品は、長期間にわたってその性能を維持し、耐久性が大幅に向上します。
優れた耐摩耗性
硬質クロムメッキは、部品の表面に強固な保護層を形成することで、摩擦による損傷を劇的に減少させます。これにより、部品は長期間にわたってその機能と性能を維持することが可能になります。特に高速で動作する機械部品や、繰り返しの摩耗にさらされる部品にとって、この特性は非常に重要です。
優れた耐食性と耐薬品性
硬質クロムメッキは、化学的に安定したクロムを使用するため、様々な化学物質や腐食環境に対しても高い耐性を示します。これにより、化学薬品や塩水などの厳しい環境下でも、部品は長期間にわたってその性能を維持することができます。この特性は、化学工業や海洋工学などの分野で特に価値があります。
膜厚と均一電着性
硬質クロムメッキは、部品の表面に均一な厚さのクロム層を形成することができます。この均一な電着性により、部品の特定の部分に必要な厚さを正確に適用することが可能です。これは、精密機械部品や特定の機能を持たせたい部分において非常に重要な特性です。
耐熱性
硬質クロムメッキは、高温環境下でもその性能を維持する優れた耐熱性を持っています。このため、エンジン部品や高温下で動作する機械部品などにおいて、長期間にわたる性能の維持が可能になります。
保油性
硬質クロムメッキされた表面は、潤滑油が留まりやすい性質を持っています。これにより、摩擦を低減し、部品の寿命を延ばすことができます。特に動きが激しい機械部品において、この特性は部品の効率と寿命を大幅に向上させます。
硬質クロムのデメリット・注意点
硬質クロムメッキは多くの利点を提供する一方で、そのプロセスは技術的な挑戦を伴い、特定のリスクを理解し管理する必要があります。以下に、硬質クロムメッキの主なデメリットと注意点について詳細に解説します。
難易度の高い処理
硬質クロムメッキは、他の表面処理技術に比べて技術的に複雑であり、その成功は精密なプロセスコントロールに大きく依存します。クロムメッキの浴槽の状態、電流の密度、温度、浴槽内のクロム酸の濃度など、多くの変数が結果に影響を及ぼします。また、均一なメッキ層を確保するためには、部品の形状やサイズに応じてこれらのパラメータを細かく調整する必要があります。
そのため、高度な専門知識と経験、そして精密なプロセス管理が要求されるため、実施するには高い技術力と設備投資が必要です。
水素脆性の発生
硬質クロムメッキのプロセス中には、電気化学的な反応が発生し、その過程で水素が発生することがあります。この水素が材料の内部に侵入すると、水素脆性と呼ばれる現象を引き起こす可能性があります。これは、材料内部の水素が引き起こす内部応力により、材料が予期せず脆くなり、亀裂や破壊が発生する現象です。特に高強度の鋼や硬化処理された材料でこの問題が顕著になることがあります。
この問題を防ぐためには、メッキ後の熱処理(水素除去処理)を施すことが一般的ですが、これには追加のコストと時間が必要になります。
硬質クロムメッキの工程
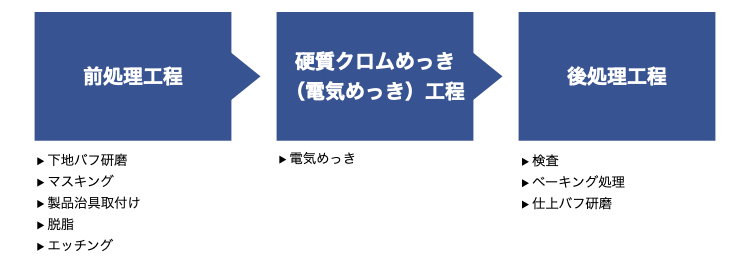
硬質クロムメッキは、その卓越した特性を実現するために、精密かつ段階的なプロセスを要求します。ここでは、この複雑なプロセスを構成する各工程について、その重要性と実施方法について詳細に解説します。
前処理工程
硬質クロムメッキの前処理工程は、最終的なメッキの品質を決定する非常に重要なステップです。この段階での作業は、メッキされる部品の表面を最適な状態に準備することを目的としています。
下地バフ研磨
表面の不純物や不均一な部分を取り除き、滑らかで均一な表面を作り出します。この工程は、メッキ層が均等に適用されるための基盤を形成します。
マスキング
メッキが不要な部分を保護するために、耐薬品性のマスキング材を使用してカバーします。これにより、必要な部分だけに正確にメッキが施されます。
製品治具取付け
メッキプロセス中に部品を安定して保持し、均一な電流が流れるように治具に取り付けます。
脱脂
表面に残存する油分や汚れを除去し、メッキ材が適切に定着するようにします。
エッチング
軽い酸洗いを行い、表面の微細な酸化層や不純物を除去し、メッキ材の付着を向上させます。
硬質クロムめっき(電気めっき)工程
前処理を経た部品は、クロムメッキ浴に浸されます。電気めっきプロセスでは、電流を使ってクロムイオンを部品の表面に結合させます。このプロセスは、メッキの厚さや質に大きな影響を与えるため、電流の強さや浴の温度、浸漬時間などの条件を正確に管理する必要があります。
後処理工程
メッキ後の後処理工程は、メッキの品質を最終的に確定し、特定の性能要件を満たすために行われます。
検査
メッキの均一性、厚さ、外観を検査し、品質基準に達しているかを確認します。
ベーキング処理
メッキ中に材料に浸透した水素を除去するために、特定の温度で熱処理を行います。これは、水素脆性を防ぐための重要なステップです。
仕上バフ研磨
メッキ表面をさらに滑らかにし、所望の光沢を得るための研磨作業を行います。
硬質クロムメッキにおけるメッキ浴の種類
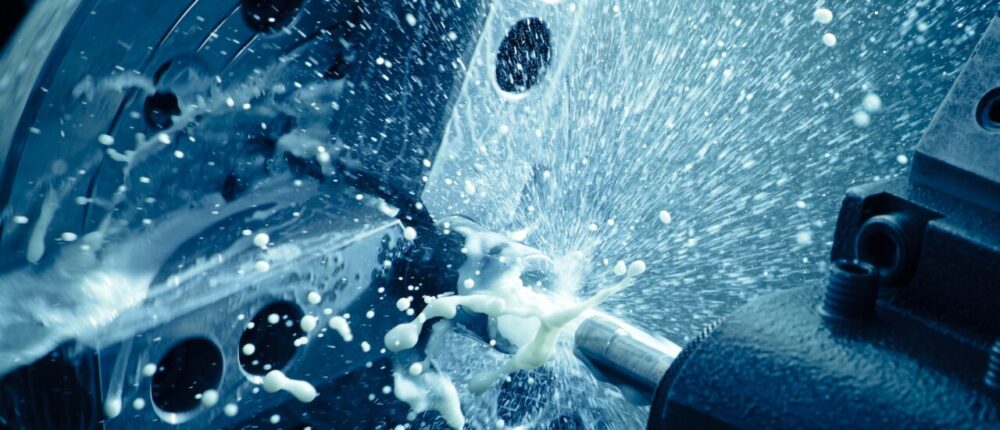
硬質クロムメッキのプロセスにおいて、メッキ浴の種類は最終製品の品質に大きく影響します。メッキ浴は、メッキの特性、効率、およびコーティングの均一性を決定する重要な要素です。ここでは、硬質クロムメッキにおけるメッキ浴の主な種類とそれぞれの特徴について詳しく見ていきましょう。
サージェント浴
サージェント浴は、硬質クロムメッキにおける最も伝統的なメッキ浴の一つです。この種類の浴槽は、安定性と信頼性に優れており、広範囲のメッキ要件に対応することができます。
サージェント浴は、クロム酸と硫酸の混合液で構成されており、これらの成分の比率を調整することで、メッキの厚みや硬度をコントロールできます。しかし、一般的にメッキ速度は比較的遅く、大量生産には向かない場合があります。
フッ化浴(混合触媒浴)
フッ化浴、または混合触媒浴は、メッキ速度を高め、より均一かつ高品質なコーティングを実現するために開発されました。このメッキ浴は、クロム酸にフッ素化合物を添加することで構成されます。フッ素化合物は触媒として機能し、メッキ反応を加速させ、より均一なメッキ層を形成します。これにより、メッキ時間を短縮し、生産性を向上させることが可能です。
また、フッ化浴は、より薄いメッキ層を均一に施すことができるため、精密な部品の処理に特に適しています。
HEEF浴(高効率浴)
HEEF浴は、「高効率」を意味するメッキ浴で、より環境に優しく、効率的なメッキプロセスを実現するために開発されました。このメッキ浴は、特別な添加剤を含むことで、メッキ速度を高め、エネルギー消費を減少させます。また、HEEF浴は、より低い電流密度で操作できるため、電気消費を抑えることができます。
このメッキ浴は、高品質なメッキを短時間で実現することが可能であり、大量生産においてもコスト効率と環境負荷の低減を両立させることができます。
硬質クロムメッキの用途例
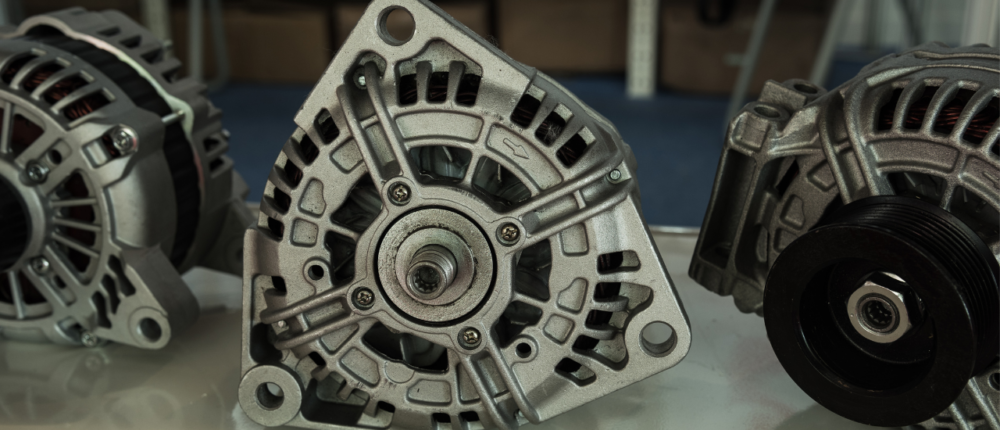
硬質クロムめっきは、クロムめっきよりも厚い被膜を生成する処理となり、金属クロムの硬さと耐摩耗性を活かした加工が可能です。
エンジン部品
エンジン部品では、摩擦、高温、圧力が絶えず作用しています。硬質クロムメッキは、これらの厳しい条件下でも部品の耐久性と性能を保持するために不可欠です。ピストンロッド、バルブ、クランクシャフトなどの部品に硬質クロムメッキを施すことで、部品の寿命が延び、エンジンの全体的な性能と効率が向上します。この処理により、エンジン部品は耐摩耗性と耐熱性が高まり、極端な環境でも高い性能を発揮できるようになります。
油圧シリンダー
油圧シリンダーは、その動作原理上、ピストンとシリンダー壁の間で高い摩擦が発生します。硬質クロムメッキは、これらの部分に施されることで、表面の滑らかさを向上させ、摩擦を大幅に減少させます。これにより、シリンダーの効率が向上し、摩耗による損傷が減少して寿命が延びます。また、メッキによる保護層は、油やその他の化学物質に対する耐性も提供し、油圧システムの信頼性と耐久性を高めます。
プラスチック射出成形金型
プラスチック射出成形業界では、金型の耐久性と精度が最優先されます。硬質クロムメッキは、金型表面に均一な硬い層を形成し、摩耗や腐食に強い表面を作り出します。これにより、金型の寿命が延び、精密な成形が可能になります。さらに、メッキ層の滑らかさにより、成形品の取り出しが容易になり、生産効率が向上します。長期的には、メンテナンスコストの削減と生産性の向上により、全体的な製造コストの削減に大きく寄与します。
硬質クロムメッキの品質項目(JIS H 8615-5品質)
.jpg)
JISに示されている品質管理項目については以下の通りです。
メッキの外観
メッキの外観は、表面は平滑で、焦げ、こぶなど使用上有害な欠陥があってはならない。ただし、つや消し仕上げ(液体ホーニング、ブラスト仕上げ、ポーラス加工など)のものについては、必ずしも平滑でなくてもよい。
メッキの表面粗さ
メッキの表面粗さは、この品質を特に重視する用途に対してだけ適用し、その品質は受渡当事者間の協定による。
メッキの最小厚さ及び許容差
メッキの最小厚さ及び許容差は、この品質を特に重視する用途に対してだけ適用し、顕微鏡断面試験方法によって試験を行い、その品質は受渡当事者間の協定による。
メッキの多孔率
クロムメッキの多孔率は、この品質を特に重視する用途に対してだけ適用し、その品質は受渡当事者間の協定による。
メッキの密着性
メッキの密着性は、砥石試験法、曲げ試験法又は引張試験法のいずれかの方法により、メッキのはく離又は膨れがあってはならない。
メッキの硬さ
メッキの硬さは、ビッカース硬さ 750 以上とする。ただし、用途によってビッカース硬さは、受渡当事者間の協定によってもよい。
メッキの耐磨耗性
メッキの耐磨耗性は、この品質を特に重視する用途に対してだけ適用し、噴射磨耗試験、往復運動磨耗試験、平板回転磨耗試験又は両輪駆動磨耗試験のいずれかの方法によによって試験を行い、その品質は受渡当事者間の協定による。
メッキの耐食性
メッキの耐食性は、この品質を特に重視する用途に対してだけ適用し、中性塩水噴霧試験方法によって試験を行い、その品質は受渡当事者間の協定による。
まとめ
硬質クロムメッキは、その優れた耐摩耗性、耐腐食性、耐熱性などの特性により、エンジン部品から油圧シリンダー、プラスチック射出成形金型に至るまで、幅広い用途で利用されています。
しかし、この高度な技術は複雑なプロセスと精密なコントロールを要求し、水素脆性などのリスクも伴います。メッキ工程の各段階は製品品質に大きく影響するため、技術者は常に厳格な品質管理とプロセスの最適化に努める必要があります。
本記事で紹介したJISの品質基準や各種のメッキ浴の種類についての知識は、硬質クロムメッキのさらなる理解に役立つでしょう。